About Wefatherm
Leading the way through innovation
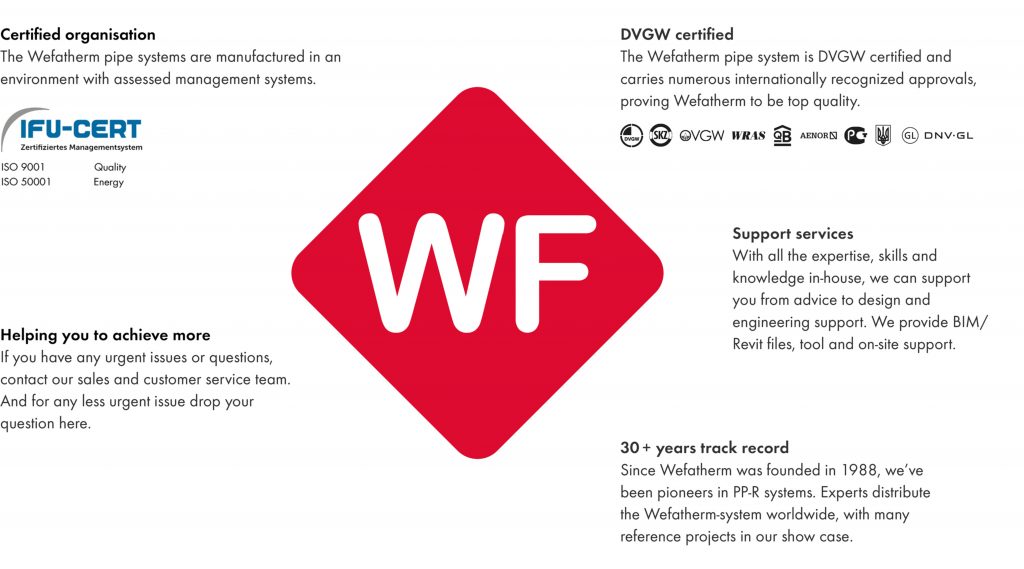
Made in Germany
With more than 30 years of experience in water supply systems, Wefatherm is always focussing on innovation, quality and dedication. Wefatherm PP-R water supply systems have been used for many years in areas of application where the pipe system has to meet high standards of durability and reliability.
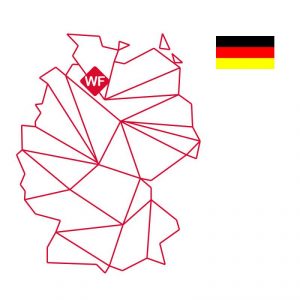
Pioneers in PP-R systems
From mould maker to manufacturer of pipe and fittings. Since its foundation in 1988 by Peter Fassbender under the name Wefa Plastic gbR, Wefatherm has always been a pioneer in PP-R pipe systems that transformed the business model from production of fittings only into a system producer for water supply systems.
German engineering and global approach
Advanced mould and process technology
From product to system innovation
Our environmental statement
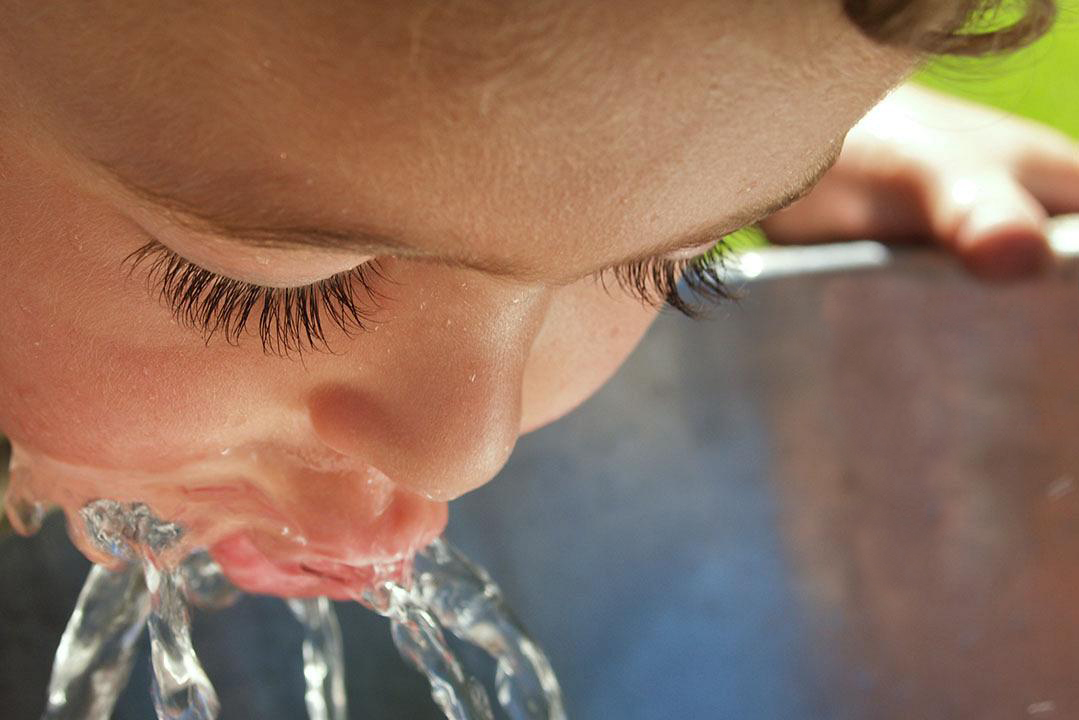
Quality management
The Quality Management System of Wefatherm GmbH has been certified according ISO 9001 for the production of water supply systems.
Internal monitoring
The Wefatherm system quality assurance starts at the gate of the factory with the receipt of raw materials. Only raw material of approved quality is processed. Processing itself is checked regularly. The modern and computer-controlled production machines and systems are checked and set by qualified and experienced personnel to ensure that they always function optimally. This gives a continuous process monitoring system, the results of which are documented.
Production monitoring
The settings of machines and the dimensional correctness of test pieces are checked carefully before production is commenced and adjustments are made if necessary. The dimensional correctness of the items produced, the setting data of the extrusion and injection moulding machines and the surfaces of the products produced are checked continuously and compared with the production specifications.
Final checks
The final products are subjected to further tests. The results of these are laid down and documented in test memoranda. Only products which have been checked and released are transferred to the warehouse. When the checks laid down in the test memoranda have been carried out and documented, the final products are released for stockholding and dispatch. Precise instructions and regular checks ensure the proper storage of the products. Packing and dispatch are regulated internally in a precise manner.